Optimizing chemical supply chain using the combination of heuristic & meta-heuristic approach.
Ottimizare — Revolutionizing Chemical Supply Chain
Category: Heuristic|Meta-Heuristic
Technology: 
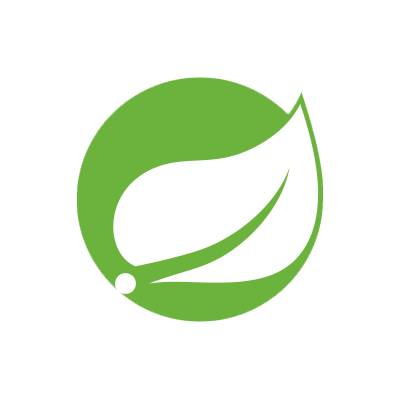
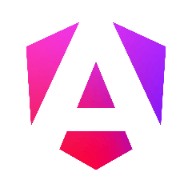
Ottimizare provides an innovative optimization solution for the chemical supply chain by combining Genetic Algorithm and Greedy Search approach. This addresses two complex NP-problems: resource allocation and the vehicle routing problem (VRP), tailored specifically for the chemical industry. The solution determines the optimal subset of orders to fulfill while accounting for constraints such as limited vehicles, storage space, hazardous goods, and the need to minimize transportation costs.
Concept of Resource Allocation
Resource allocation is the complex combinatorial problem in the transportation management which involves multiple objectives. Multi-objective optimization involves a complex problem which may have conflicting objectives and are required to be fulfilled appropriately.
In general, the mathematical representation for multi-objective problem is provided as:
- f(x) = min (x1, x2, x3, …, xn)
- f(x) = max (x1, x2, x3, …, xn)
These are subject to certain constraints
- m ≤ p || n ≥ q
- l = r
Where, `m`, `n` and `l` are the independent variables and `p`, `q`, `r` is the decision variable. The goal of resource allocation is to determine the optimal set of orders on = {x1, x2, x3, …, xn} such that the fitness value is maximized while satisfying constraints `a` (xi = k) and `b` (xi ≤ k). In the chemical industry, the complexity of such problems is increased due to the nature of resources, particularly in hazardous goods transportation. These factors significantly enhance the challenge of finding optimal solutions.
Fundamental Decision Variables
Decision variables are often referred as controllable variables, play an important role in influencing the solution space of the algorithm. Following are the decision variables:
- ov set of orders / order matrix to be delivered by vehicle V.
- vn no. of vehicles.
- ki type of delivery for node i.
- dij distance between node i and node j.
- mi demand at node i (in case of drums-oriented transportation).
- pv allowed number of drums for vehicle V.
- qv allowed number of bags for vehicle V.
These decision variables define a specific scenario or instance to determine best set of orders to be served by each vehicle v. Among them pv and qv, are two essential parameters that influence the chromosomes in our genetic algorithm.
In the transportation of chemical goods, vehicles typically handle either bags or liquid drums, depending on their capacity and type. The variable ki determines the type of delivery, either it is drum-oriented (solely drums transportation) or bags-oriented (solely bags transportation).
- Drums: Sizes vary, but commonly used capacities includes 200 kg, 230 kg and 250 kg.
- Bags: Common sizes include 25 kg, 50 kg, and 100 kg, though these can differ based on the nature of the stock.
The variable mi refers to the total product quantity demanded by the customer, while variable vn is total number of available vehicles. For this algorithm, we assume a 20-ft GP (General Purpose) container as the standard vehicle, which can be adapted to other configurations if necessary. A 20-ft GP container typically accommodates:
- Drums: Up to 80 drums (20 pallets, 4 drums per pallet).
- Bags: Up to 640 bags (20 pallets, 32 bags of 25kg per pallet).
Fitness Evaluation
In case of chemical goods transportation, there are three primary constraints: 1) Not exceeding of allowed number of drums. 2) Not exceeding of allowed number of bags. 3) No dangerously reactive combinations. The third constraint enhances the intricacy of the problem. The guidance for dangerously and non-dangerously reactive combinations were obtained from American Institute of Chemical Engineers, 2008. To further elaborate the complexity, let’s understand through an example; Crotonaldehyde chemical belongs to group XIX category, aldehydes, is incompatible with group I. Generally, chemicals which falls under group XIX are compatible with group I; however, the case is different for Crotonaldehyde. Group XX chemicals are generally incompatible with group V, caustics; however, butyl alcohol is compatible with Caustic soda, 50% or less (V). These examples just depict the nature of complexity.
We can, in simple words, infer that particular group which may not be compatible with another group can be compatible with specific chemicals or a particular group which may be compatible with another group can be incompatible with specific chemicals. So, we have to logically make our algorithm distinguish dangerously and non-dangerously reactive combinations.
If the generated chromosome does not meet three specified conditions; then the solution is either discarded or ranked bare-minimum. As the chromosomes are created, they are ranked based on their fitness value. Any individual which violates the specified constraints are discarded.
Epitome
Ottimizare is a two-phased approach:
- First phase: The algorithm identifies an optimal subset of orders.
- Second phase: It determines the best route, minimizing the overall distance travelled and costs incurred.
Reference: Time Series & Heuristic Application In Supply Chain.